Table Of Content
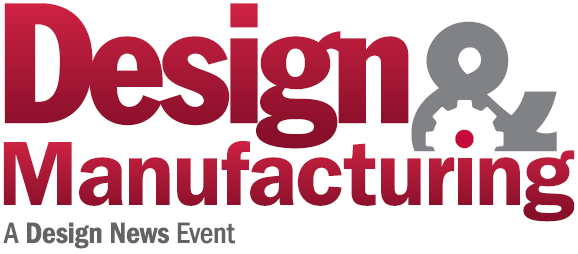
Enclosures can be made out of metal, plastics, polymers, and even composites. DFM analysis compares each material against the product’s functional requirements and suggests the best one. Incorporating surface mount technology (SMT) for components on printed circuit boards (PCBs) to streamline assembly.Designing PCB layouts with good thermal management to prevent overheating. Designing product enclosures with minimal undercuts for easy molding in plastic injection processes.Employing snap-fit or clip-on mechanisms for easy assembly of product parts.
A Guide to Design-for-Manufacturing (DFM) Principles
When it comes to design priorities, there may be tension between those that prioritize utility and those that prioritize efficient manufacturing. This is why, when designing with both user demands and manufacturability in mind, it becomes necessary to modify the design iteratively. Cutting-edge materials can boost product performance, but they can also be hard to come by or expensive. Finding the sweet spot requires looking at several materials that are affordable, have acceptable performance and are readily available. Developing a design for manufacturing strategy is the first thing product owners should focus on when creating a new product. The earlier you focus on DFM techniques, the more time and money you can save in the long run [1][2].
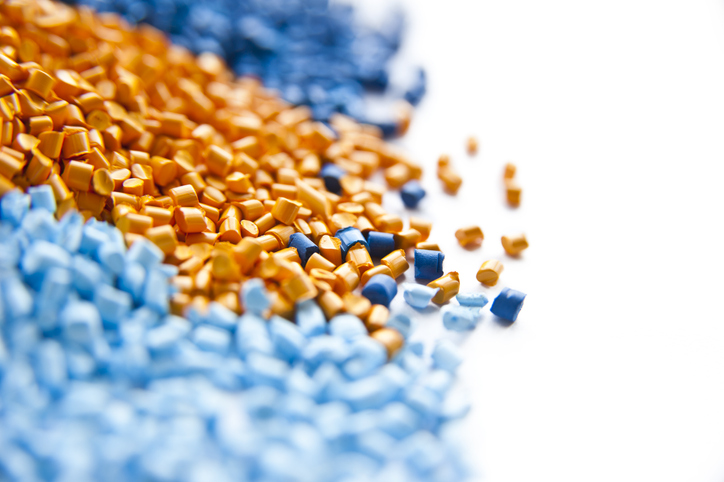
DFMA
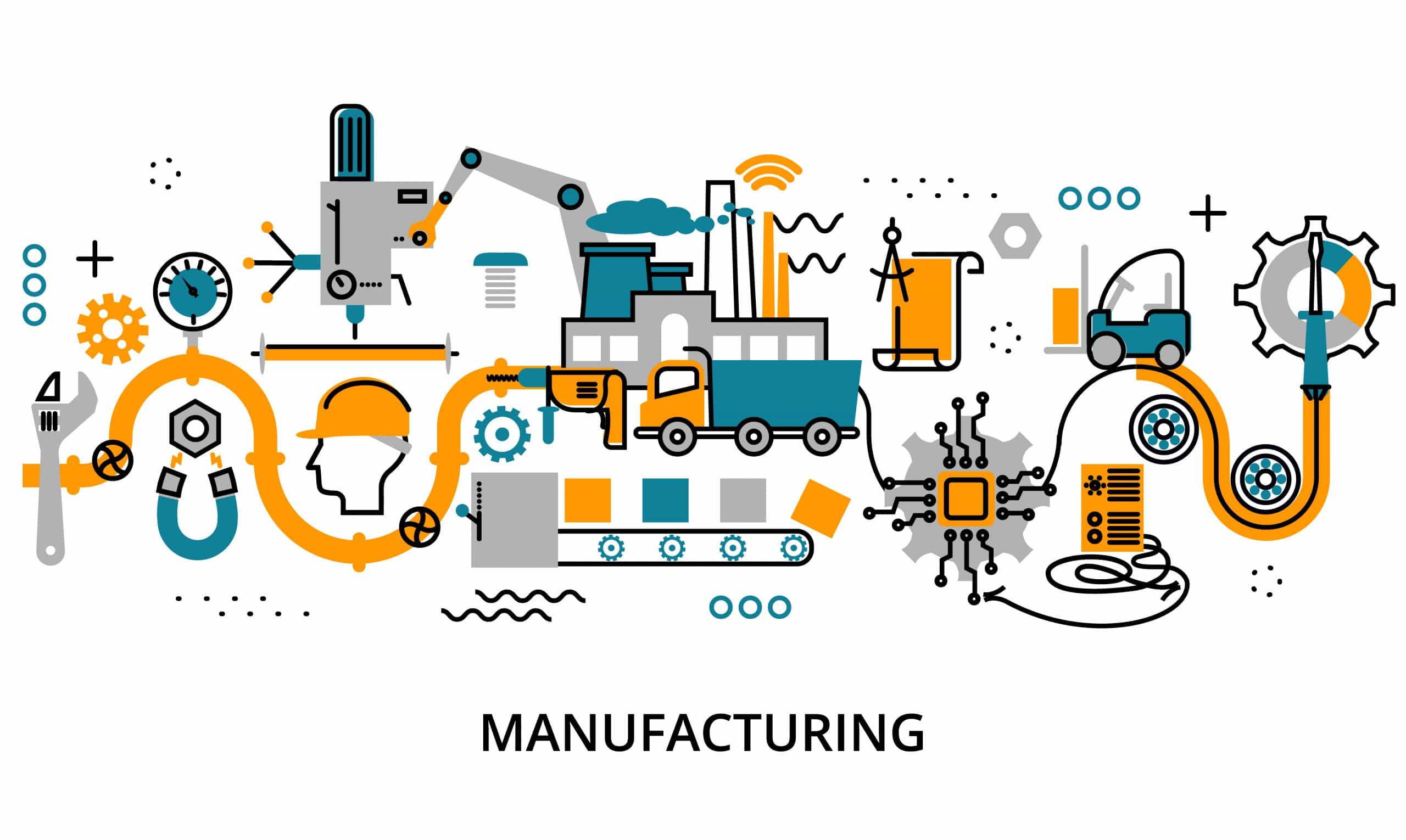
Some examples include DFMPro, Boothroyd Dewhurst, and Autodesk's DFM tools. Xometry makes no representation or warranty of any kind, be it expressed or implied, as to the accuracy, completeness, or validity of the information. Buyers seeking quotes for parts are responsible for defining the specific requirements for those parts. DFM focuses on reducing the required number of manufacturing operations while still meeting the product’s functional requirements.
Benefits of DFM
DFM has various advantages, including lower production costs, higher product quality, and a shorter time to market. DFM is a crucial aspect of the product design process, aimed at reducing production costs while maintaining performance. By considering factors such as the number of parts, standardization, modular assemblies, and manufacturing technology, manufacturers can optimize their production processes and ultimately achieve success. The benefits of DFM, including reduced production costs and improved performance, make it a valuable tool for any manufacturer looking to succeed in today’s competitive market. Design for manufacturing (DFM) has its roots in the post-World War II era when companies were looking for ways to improve their competitiveness in the global market. At the time, manufacturers were facing increasing pressure to reduce costs, enhance the quality of products, and increase production efficiency while also facing increased competition from other manufacturers.
Design for Manufacturing With 3D Printing
8th annual Italian Design Day in the USA: “Manufacturing value – inclusiveness, innovation, and sustainability” - Ministero degli Affari Esteri e della Cooperazione Internazionale
8th annual Italian Design Day in the USA: “Manufacturing value – inclusiveness, innovation, and sustainability”.
Posted: Tue, 12 Mar 2024 07:00:00 GMT [source]
However, previously, this referred to two distinct practices, DFM and Design for Assembly (DFA). Another obstacle to DFM implementation is the lack of communication and collaboration between design and manufacturing teams. This can lead to designs that are difficult or expensive to manufacture, increasing production costs and reducing profitability. Design for manufacturing (DFM) contributes to product innovation and efficiency by integrating manufacturing considerations into the design process. This approach allows for the identification and elimination of potential manufacturing constraints early on, fostering innovation through more feasible designs. By optimizing designs for manufacturing, DFM enhances efficiency by streamlining production processes and reducing costs.
Additional Requirements
All uploads are secure and confidential, click to check our IP Protection Policy. You can also contact us () to sign a NDA before sending any design files to us. If it prompts that the file format does not support uploading, please compress the file into a zip file before sending it. Whether it's a one-off prototype made or a batch production of thousands, LEADRP is ready to support your project. For example, if you understand the writer's intent, it's much easier to make the corrections in the text.
This schedule enables careful examination and modifications to ensure that the finished design is best suited for economical and successful manufacturing procedures. Sometimes these are industry standards, others are third-party standards and some are internal, company-specific standards. You'll note that many of the same questions he asks with regard to process will also come up under the 'Design' heading.
This is, of course, done within the bounds of limitations like budget, material options, and the target markets. Design for manufacturability is a wide-ranging methodology that branches into multiple areas of the product development lifecycle. Therefore, it is important to understand its main goals to provide DFM engineers with a clear framework to work within. DISHER takes a design-first approach to product development, engineering, and manufacturing. We help our clients by applying DFM to every product development project we work on saving valuable time and money.
This can be achieved by selecting high-quality materials, using robust design principles, and considering the product's expected operating conditions during the design phase. This involves reducing the number of parts, eliminating unnecessary features, and designing parts to be multi-functional. Simplified designs are easier and less expensive to manufacture and assemble. The early stage of the design process is the best time to implement DFM because it allows designers to make changes quickly and at a lower cost. Changing the design later is particularly difficult when it requires retooling. Thorough manufacturability evaluations are usually the first step in integrating DFM into the design.
The use of DFM in PCB manufacturing is primarily driven by the ongoing need for miniaturization, resulting in numerous design constraints. It also means that designers and manufacturers must work together more closely to achieve further improvements in this maturing technology. The further along a design is in the product development process, the more expensive changes become, making it critical to address design issues as early in the process as possible. Cost, performance, lead time and scalability are some of the technical issues and trade-offs that come into play when choosing materials and processes for DFM.
It simulates the filling, packing and cooling stages, which helps to reduce cycle times and errors. Another strategy is to encourage communication and collaboration between design and manufacturing teams. This can be done by involving manufacturing teams in the design process from the beginning, allowing them to provide input and identify potential manufacturing issues early on. Design for manufacturing (DFM), or design for manufacturability, is a set of practices for designing products that make them easy to manufacture.
They can be combined into a single production method though, called Design for Manufacturing and Assembly (DFMA). In this article, we’ll be focusing on DFM, so let’s start from the beginning.
In this scenario, the customer had trouble getting the flatness just right and encountered ejection problems when molding. Due to its ability to reveal your processes and compel you to pay close attention to detail, simulation has become practically indispensable in modern times. It captures subtleties, and in doing so, you gain a better understanding of your organization.
Data taken in real-time can be used to optimize products in the field through software changes or maintenance requests. Historical data collected by IoT systems in manufacturing or from the product in operation can guide more efficient maintenance schedules and further inform the digital twin. These are just some of the questions that can be answered with these digital technologies. With a large number of manufacturing processes and complex cost drivers, DFM product modeling has, historically, been a serious analytical challenge. Today, digital manufacturing simulation tools are enabling engineering organizations to institute deep DFM modeling that would have been computationally prohibitive in the past. Design for manufacturability or design for manufacturing (DFM) is the engineering process of designing parts to optimize their manufacturing ease and production cost, given their form, fit, and function needs.
No comments:
Post a Comment