Table Of Content

Suppliers have a wealth of experience and understanding of their materials and manufacturing processes. Utilizing standard components wherever possible can also significantly reduce manufacturing costs and lead times. Standard components are readily available and often cheaper than custom parts.
Cost reduction
DFM principles help designers keep PCB specifications within a layout, which becomes more important as the size of PCBs decreases. For example, incorporating existing components into a smaller design often results in issues like acid traps and insufficient edge clearance. Maintaining the high signal integrity needed by today’s PCBs also requires manufacturers to place and route circuits according to a design that best facilitates transmitting those signals. Specific techniques for testing and designing reliable products include failure mode and effects analysis (FMEA) and fault tree analysis (FTA).
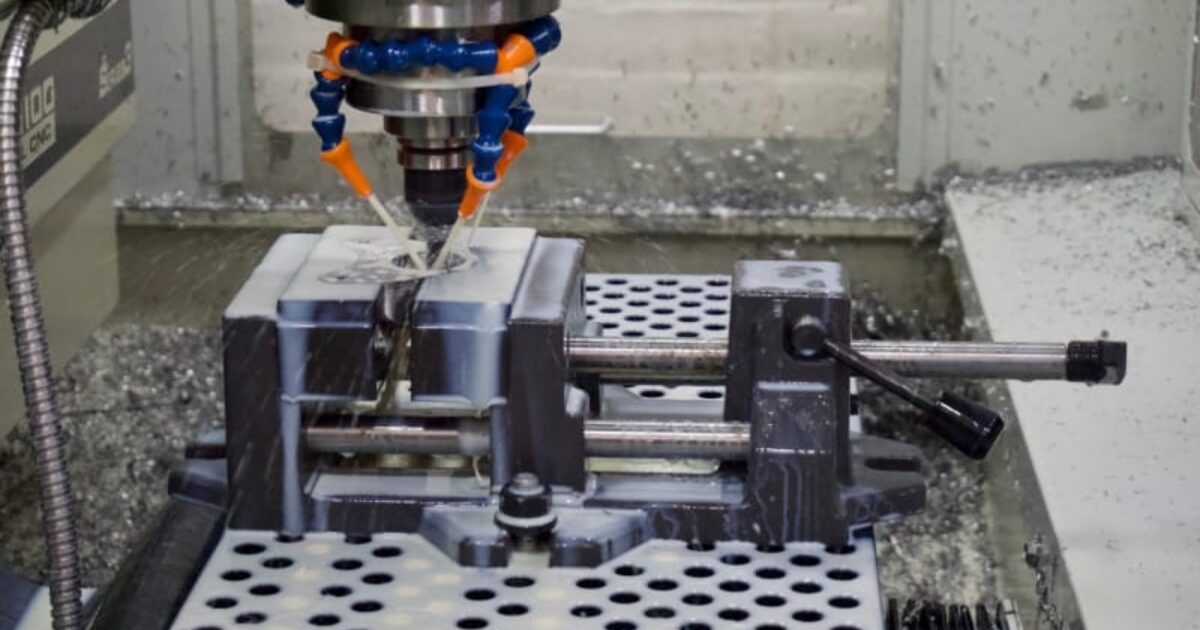
Designing the Manufacturing Process for a Composite Countersink
Modular design is another key aspect of serviceability, as it allows repair technicians to replace only the failed part. For example, they should be able to replace just a faulty temperature sensor on a central air conditioner instead of also replacing its PCB. Product design can also help with breakdowns by allowing easier access to parts most likely fail first. For example, accessing a vehicle’s spark plugs is usually much easier than accessing fan belts because plugs tend to wear out faster than belts. A part should only be separate from the rest of the product if a specific reason exists for doing so.
OUTCOMES OF AN EFFECTIVE DFM
They also allow for easier replacement during the product's maintenance and repair. The expected operating environment greatly affects a product’s quality standards. A PCB that needs to run in a dusty area must be built to higher specifications, especially with respect to heat tolerance and airflow.
Design decisions that are based on holistic sustainability KPIs will result in massive efficiency gains for the product in the real world. Combining the real and digital worlds makes it possible to integrate and digitalize the entire value chain. This delivers a digital thread that serves as the foundation for collective intelligence, connecting workflows and processes along the value chain. It can also provide designers with access to a comprehensive digital twin informed by simulation results and production data, material information, supplier and product carbon footprint data, etc. Design for manufacturing is just one of the areas where 3D printing can benefit the manufacturing process. Watch our webinar to see how leading manufacturers leverage 3D printing to save money and shorten lead times from design to production and learn about five ways to use 3D printing in your manufacturing workflow.
NiMH vs Lithium Ion Batteries: A Comprehensive Comparison for Engineers
“Therefore we’re within the envelope of what was sized 15 years ago when the production system launched,” he says. Speaking during a first-quarter briefing on 25 April, Airbus chief executive Guillaume Faury pointed out that the original sizing of the A350 production system was centred on a 13-per-month build rate. But recent strong order activity for the twinjet family has generated a backlog of 685 aircraft – including 415 baseline -900s as well as 55 of the new A350 freighter.
Keywords:
The design study revealed a production time of about 5 hours and 35 minutes, and a production capacity that corresponds to one engine every seven minutes. The use of DFM techniques led to the discovery of opportunities to alter the production process in order to lower overall costs. Throughout the assembly process, it became clear to the component supplier that these milling and non-pass bores were unnecessary for the assembly to continue.
At Imagineering, we’re committed to providing our clients with the best possible service and support from design to production. Our team of experts is well-versed in DFM and can help you identify and solve any potential issues in your PCB design early on. If you are ready to get started, contact us today to receive a custom quote tailored to your specific needs.
Importance of Communication and Collaboration Between Design and Manufacturing Teams

In this sense, suppliers can become strategic partners, filling in the gaps and helping design teams make informed decisions that lead to more effective and efficient production processes. One strategy is to educate design teams about the benefits of DFM and the importance of designing products with manufacturing in mind. This can help to shift the mindset of design teams and reduce resistance to change.
Enterprises can reduce manufacturing delays, enhance product quality, and eventually obtain a competitive advantage in the market by incorporating DFM principles into the design process. Improving a product is not the final step in the design process, but rather a continuous journey that extends long after the product is made. Integrating sustainability goals into product design is making that a reality for every company. With simulation data, testing results, and a more concise digital twin, uncovering any performance gaps, reliability issues, and refurbishment and upgrade paths for products becomes much easier. Design for manufacturing reduces costs and time to market, and produces significant improvements in quality and reliability. It is imperative to always consider DFM principles when developing a new component or product.
However, DFM principles require designers to ensure that quality goals are reasonable, as manufacturing costs are also a critical consideration. In Design for Assembly, the designers must always keep the ease of assembly in mind. Simplifying assembly steps will reduce the costs, effort and time put into a product. For instance, reducing the total number of parts in the assembly and designing out fasteners will speed up the assembly process significantly and increase the overall efficiency. Once the detailed design is complete, it is time to validate the product’s performance. Validation covers many workflows and engineering domains to ensure the product functions as expected.
Latest from Design & Manufacturing (D&M) Canada 2023 - Design News
Latest from Design & Manufacturing (D&M) Canada 2023.
Posted: Sat, 11 Nov 2023 03:07:12 GMT [source]
The core purpose of design for manufacturing is to minimize the production cost of a design as much as possible. In most cases, product development begins with a vague idea with no practical limitations. It may be impossible to manufacture due to several reasons like high costs, design complexity, material unavailability, etc. DFM analysis looks at product development from these angles and adds credibility to the product designers’ ideas and investors’ stakes.
One of the most important parts of DFM is incorporating it early on in the product development phase. Using DFM early on in the development cycle helps to match design choices with production capabilities and restrictions, which in turn reduces the possibility of expensive adjustments later on. By standardizing procedures, terms and design principles, you can reduce ambiguity and maximize clarity, which in turn facilitates effective teamwork and problem resolution.
Using quality standardized parts can shorten time to production as such parts are typically available and you can be more certain of their consistency. Finally, let us discuss the applications of design for manufacturing in the context of injection molding. They allow engineers to ascertain whether the design is capable of withstanding its environmental conditions and are instrumental in changing the design according to manufacturing requirements. The use of modular designs is another technique widely adapted by DFM engineers.
Design optimization is among the top designs for manufacturing principles. Design for Manufacturing (DFM) is one of the most critical aspects of product development. It is the important connecting link between conceptual design and manufacturing and can have a massive impact on a product’s performance and cost.
No comments:
Post a Comment